What Is Closed Loop Recycling?
Closed Loop Recycling is an environmentally and economically sustainable concept that has been around for decades. It involves the collection, recycling, manufacturing, and selling of a recycled product as new in a continuous cycle. Aluminum, glass, and plastics are all examples of recyclable commodities used in closed loop systems.
Aluminum is one of the most recognized commodities that is used in a closed loop recycling system. According to Earth 911, nearly 70% of each aluminum can made in the US comes from recyclable materials.
Some benefits of closed loop aluminum recycling include:
- A sustainable way to remove outdated products
- It helps reduce the cost of manufacturing new aluminum cans
- Eliminate recyclables from being added to landfills, creating a more sustainable environment for future generations
Although we are all responsible for the collection of aluminum containers for recycling, there are a few types of businesses that collect the most volume of aluminum to recycle. They include recycling centers, municipalities, bottlers, brewers, and distribution centers.
What Equipment Do Aluminum Recyclers Use?
Recycling aluminum once its collected can be a time consuming and difficult task. The containers must be drained, baled, and shipped to be processed into new products. Let’s take a look at the innovative equipment that each one of these industry sectors often uses to complete closed loop aluminum recycling.
Recycling Centers/Municipalities:
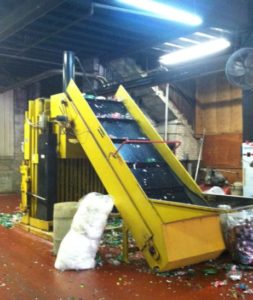
Harmony’s T60XDRC in use at a recycling center.
These recycling centers act as regional hubs for collected aluminum to be brought and sorted in large volumes. Often times, the aluminum is sorted into totes and dumped into a hopper and onto a conveyor. The conveyor takes the aluminum into an automatic baling system like Harmony’s T60XDRC Automatic Baler.
The System Ten Sixty Automatic Baler can be configured as a unique rear feed baler for use in high capacity situations like this, when space is at a premium.
Harmony’s T60XDRC doesn’t require any material preconditioning and cycles automatically as the conveyor loads the material into the baler. The dense bales produced are mill-sized and are ejected smoothly with dual hydraulic ejectors.Harmony’s innovative T60 solution has quickly become the choice of community recycling centers and municipalities when it comes to large capacity automatic balers. With an immediate ROI and long life expectancy, its easy to understand why.
Bottlers and Brewers:
Some recyclers of aluminum have the need to drain the liquid from the aluminum container prior to it being baled. Bottling facilities initially consider investing in this equipment to help them manage out-of-date product and adjust internal SKU’s.
Owners also prefer to have product destruction equipment right at their bottling factory, eliminating the need to transport the full bottles and cans to a third party location. All of the product destruction can happens at the bottling facility so management can have total control over the process, minimize the cost, and bale the recyclables to maximize their revenue.
The size, shape, and contents of the beverage containers that are drained and baled vary across the industry. Regardless of the demographic or volume, Harmony is able to provide a safe, efficient, and affordable solution with our full line of beverage extraction balers.
For smaller breweries and facilities, our current Product Spotlight, the ExtractPack BCB2003 provides an affordable solution for smaller volume with hand-fed front loading of the product. It also fits into areas with low ceiling height.
Other larger facilities require the greater than 1.5 FTE savings produced by our SSHB GEN 1 or SSHB GEN 2 beverage extraction machines. The GEN2 is a mill-sized baler that uses an incredible 25,000 aluminum cans in its baling process!
Distribution Centers:
Some extremely large volume distribution centers do not have issues with operational space or with the need to drain the aluminum prior to baling it. For these situations, Harmony proudly offers its HM60 Horizontal Baler.
This powerhouse baler produces 700 lb, mill-sized bales of aluminum. It has automatic bale decompresson, remote mounted controls, a hydraulic door latch, and a 7″ color HMI that allows the user to select the commodity being baled.
With the optional conveyor and large 54″ x 40″ feed opening, the HM60 handles large quantities of aluminum with ease. It improves workplace appearance and safety, while increasing profitability and efficiency.
Is Your Business Ready To Close The Loop?
If your business has the need to recycle aluminum, let Harmony help you understand what type of baler best suits your business model. We work with you to form a true partnership approach and will help educate you and your staff on the installation, operation, and maintenance of your equipment. If you are ready to close the loop on aluminum recycling, give us a call at 507-886-6666 or Contact Us today!