Digital Transformation Conference
Werner Electric has been the supplier for innovative OEM’s like Harmony Enterprises for decades. As a part of their wider mission, Werner offers unique opportunities for educational seminars at their Cottage Grove, MN headquarters.
This past Thursday, September 26, Werner hosted their 2019 Digital Transformation Conference. This informative event was a one day conference of educational sessions on solutions and strategies for using data and technology to optimize and modernize business operations.
It focused on the way that businesses and manufacturers can utilize digital technology as a connected enterprise, in their own production processes, as well as to benefit their customers.
The digital transformation in manufacturing allows businesses to utilize predicative analytics, expand data storage, and better analyze unstructured data. This has been proven to lead to opportunities for:
- Faster time to market
- Lower total cost of ownership
- Improved asset utilization
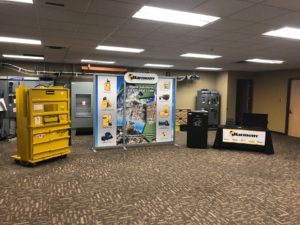
Harmony was proud to be the featured guest at the Werner DTX Vendor Showcase.
Harmony Enterprises was honored to be the featured partner in the Vendor Showcase and one of the main speakers at the beginning of the day. Set up in Werner’s innovation center, Harmony brought several waste handling and recycling solutions to demonstrate, including our M42BC Stockroom Baler, our SmartPack Automatic Compactor, and our Insite Technology. We also shared our company’s Capability Statement and SmartyTheSmartPack USB drives with our company videos on them.
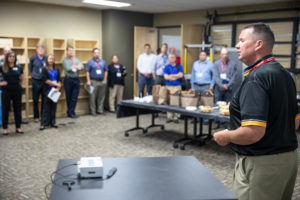
National Sales Manager, Nick Roberts, shares Harmony’s success with wireless monitoring of compactors.
In attendance from Harmony as VP of Operations, Ramon Hernandez, National Sales Manger, Nick Roberts, Engineering Manager, Isaac Kruse, and New Business Development Manager, Lane Powell. Mr. Roberts addressed the audience of nearly 50 participants in a welcoming address about the history of Harmony Enterprises and how Harmony uses connected enterprise for the betterment of all.
Throughout the day, attendees were able to stop and learn more about Harmony’s Core Values, history, products, and services. Several guests shared their own stories on how they would like to incorporate connected enterprise into what they do and how Harmony’s solutions and story might better help them achieve their goals.
Harmony As A Connected Enterprise
How does Harmony use digital technology in our connected enterprise?
Production/Engineering
In production, Harmony uses kitted electrical boxes manufactured through the innovative design center of Werner’s Modiflex department. For Harmony, this cuts down on production time, guarantees product accuracy and conformity, as well as reduces time to market.
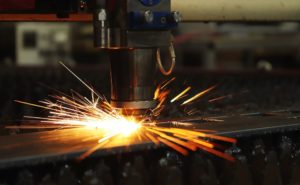
Harmony’s CNC Programmers and Operators utilize SigmaNest software to help them improve efficiencies in fabrication.
Harmony also utilizes software throughout the plant floor to help with the clocking in and clocking out of each manufacturing job. This enables Harmony to track the exact amount of hours needed in each BOM and router. It also helps us track any rework and overhead costs associated with each product. Improving our labor efficiencies helps us to pass savings on to our customers. Harmony also uses a universal software system for production scheduling and tracking of jobs.
In Engineering, Harmony uses SigmaNest Programming in our CNC department for our plasma table. These programs allow us to make exact fabrication of parts with minimum scrap. We also use Vault Thin Client to store and manipulate designs, drawings, and documents. Having universal storage systems helps to streamline processes.
Sales/Marketing/Customer Service/Accounting
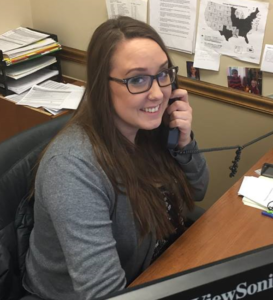
Lindsey Barrett, Customer Service Manager, uses data gleaned from automated surveys to track and improve customer satisfaction.
Our Sales, Customer Service, and Accounting Departments use an integrated CRM for sales orders, invoicing, and customer service.
Our Customer Service Department satisfies one of our ISO requirements for customer satisfaction using an automated survey tool that links back to the interdepartmental CRM.
How Our Customers Benefit
Using PLC’s in our equipment with Rockwell and Allen Bradley components gives our customers confidence that our machines will run at the optimum level.
Our Insite Technology provides real time data on our indoor and outdoor compactors, as well as our balers. On compactors, customers save on FTE’s related to waste, waste accessories, and hauling costs. They receive SMS text or email messages notifying them and haulers when the compactors are partially full, full, or need to be serviced.
With our smart balers, our customers achieve desired bale weights and densities using load cell technology. This helps them to add recycling revenue where their once was expense. All of our Insite Technology helps to plan for preventive maintenance by keeping track of cycles, cycle time, and more!
The most obvious benefits of Harmony’s Connected Enterprise for our customers is the faster time to market, lower equipment and service costs, and long lasting product life.
Get Connected With Harmony Today!
Harmony Enterprises is proud to live out our Core Value of Innovation and use digital technology to transform the way we do business. If you would like to learn more about our connected enterprise, our full product line, or service and parts, please call us at (507) 886-6666 or Contact Us to get connected with Harmony today!