Harmony Enterprises, Inc. has reached a huge milestone! After a two year process, on January 14, 2014, Harmony Enterprises, Inc. received ISO certification. For those who participated on the ISO Team it has been a rewarding and interesting journey that does not stop with receiving certification. In one year, the auditor will return to verify that we continue to comply with the ISO standards, and thereafter, certification is renewed by external audit every three years.
What is ISO?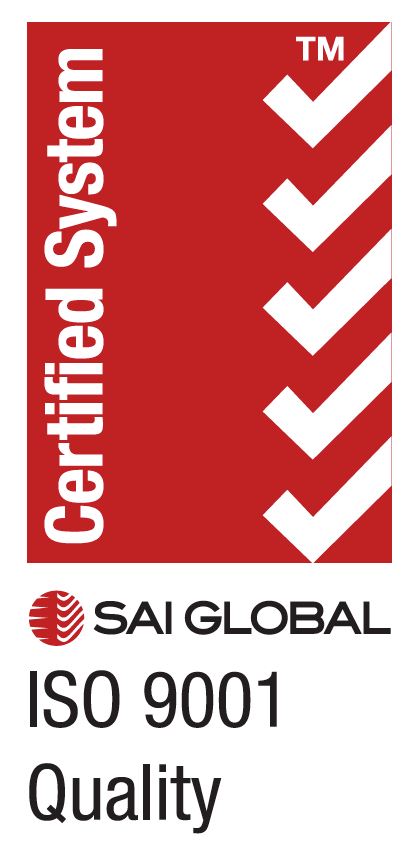
ISO 9001:2008 specifies requirements for a quality management system where an organization needs to demonstrate its ability to consistently provide product that meets customer and applicable statutory and regulatory requirements, and aims to enhance customer satisfaction through the effective application of the system, including processes for continual improvement of the system and the assurance of conformity to customer and applicable statutory and regulatory requirements.
What does ISO Certification mean for Harmony Enterprises?
Harmony Enterprises, Inc. has always strived to provide the best quality equipment in our industry. By making the decision to become ISO Certified, it reinforces our commitment to quality. ISO is a checks and balances system, that requires us to follow procedures, identify any areas of concern, promptly address these concerns with corrective or preventive actions, and is supported with on-going internal audits throughout the year. The procedures and processes that are required by ISO will help Harmony Enterprises to continually improve not only our products but how we operate and service our customers.
How Harmony Enterprises got ISO Certified
Two years ago, a team within Harmony Enterprises was selected by upper management to take training from an outside consulting service, Enterprise Minnesota. The training began with helping us understand ISO and how it will benefit Harmony Enterprises, along with developing our Quality Manual. As we developed our Quality Manual, we also had to begin developing the required procedures and polish procedures and processes that we already had in place to meet the requirements of ISO 9001:2008 standards. It was the responsibility of the ISO Team to educate the rest of the employees, implement the required procedures, as well as help management understand their rolls in ISO Certification. One of the key tools offered by ISO is Internal Audits. This tool allows trained auditors to go to a department or area and audit the processes as they relate to the ISO standards and our quality expectations. In mid-September Harmony Enterprises had our Stage 1, also known as Readiness Audit, where an external auditor came to our facility and verified that we had all the basic requirements in place to move forward with the Stage 2, or Registration Audit. The Registration Audit took place in mid-December. It was a three day process, where the external auditor came to our facility and audited all of our procedures to the ISO 9001:2008 Standards. The auditor spent time with people from every department of our company, ensuring that we had all the proper procedures in place and functioning to meet the requirements of the standard. Once all of the requirements were verified to be in conformance with the ISO 9001:2008 Standards the auditor recommended us for certification.
Thank you to all of the staff at Harmony Enterprises, and especially the ISO Team, who worked so hard to achieve this goal. We are proud to have achieved this ISO Certification, and will continually work on processes for continual improvement of the system.