Harmony Passes ISO 9001:2015 Surveillance Audit
This past week, Harmony Enterprises successfully completed its ISO 9001:2015 surveillance audit. According to iso.org, ISO 9001 “sets out the criteria for a quality management system and is the only standard in the family that can be certified to (although this is not a requirement). This standard is based on a number of quality management principles including a strong customer focus, the motivation and implication of top management, the process approach and continual improvement. It can be used by any organization, large or small, regardless of its field of activity. In fact, there are over one million companies and organizations in over 170 countries certified to ISO 9001.”
In short, the ISO certification process allows manufacturers like Harmony Enterprises to use these stringent standards to produce consistent quality goods and services, resulting in customer satisfaction.
Providing A Positive Impact
Although Harmony Enterprises uses the ISO 9001 standard to continually improve and adapt, it ultimately helps us to pass the benefits of quality and longevity of our balers and compactors onto our customers. ISO requirements help us to maintain a laser focus on customer satisfaction and the quality processes we use to manufacture our equipment and operate our business. We consistently perform unbiased internal audits in every area, creating corrective actions to improve any inconsistencies or gaps.
Here are just a few ways that our ISO 9001:2015 certification helps our partners:
- It requires that we understand customer and vendor needs and expectations and clearly document them.
- It helps us to ensure that the entire sales process is geared to provide the right solution for each specific customer, taking into account use case, site reviews, custom specifications, electrical requirements, and more. Harmony manufactures the widest range of solutions on the market, as no one solution is right for every business.
- We maintain accurate calibration of all tools, leading to consistent fabrication of our quality machines.
- We provide quality control inspections in every area of production, removing and correcting any items or processes that are non-conforming to our standards of excellence.
- All of our continually improving processes help us to create improved efficiencies and quality in the making of our products, which result in more lean manufacturing, allowing us to pass along the cost and time savings to our customers.
Thanks To Our Team
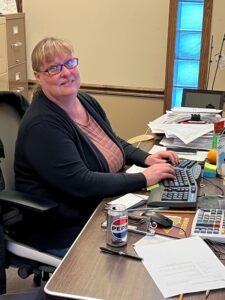
Office & ISO Manager, Lana Soppa
Our ISO 9001:2015 certification would not be possible without the leadership of our Office Manager, Lana Soppa, our President, Ramon Hernandez, our internal auditors, and dedicated employees. We would like to thank everyone involved in our surveillance audit for their work in helping us to pass with flying colors. We will work tirelessly to live up to this important standard, which is one of the reasons Harmony was named Family-Owned Manufacture Of The Year in 2020 and one of the Best Minnesota Manufacturing Companies by BestStartup.us in 2021.
Contact Your ISO Certified Baler & Compactor Specialists
If you would like to learn more about our ISO process, how it helps us to serve satisfied customers around the globe, or about our industry-leading products and services, please Contact Us or call us at (507) 886-6666 today. We look forward to working with you to understand your needs and expectations, and providing you with the right waste and recycling solutions for your business!