Harmony’s Robotic Welder Provides Efficiency
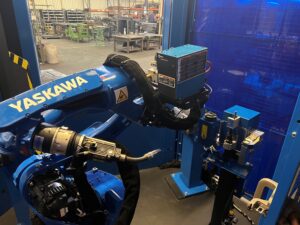
Harmony’s robotic welder provides perfect tilt and repeatable consistent welds for our baler and compactor parts.
Increased efficiency through process automation is a constant goal for any manufacturer. For Harmony Enterprises, the third generation, family-owned manufacturer of recycling balers and trash compactors, this is no exception. This time last year, we shared that our new robotic welder was ordered and would soon be in use making parts for our quality machines. Since that time, our robotic welder has been installed, our employees have been trained, and we are up and running. We are thrilled with the benefits provided by this innovative tool!
How Does A Robotic Welder Increase Efficiency?
Harmony’s robotic welder is currently used to create larger quantities of component parts. This frees up our team of welding male and female welding professionals to use their superior skills to weld the chambers, floors, and sides of our long-lasting equipment.
With this in mind, there are several ways that Harmony’s robotic welder helps to increase our production efficiency. Here are just a few:
Flexibility – The ability for the robotic welder to complete a variety of repetitive tasks over the course of a shift is useful for a business like ours that offers the widest range of products and associated parts on the market.
Increased Productivity & Throughput – Automated welders work at a greater efficiency compared to humans. That’s perfect when we are dealing with quantity runs of component parts. Our welding staff can spend their time on more important jobs while the robot cranks out batches of a variety of precision parts.
Precision & Quality – Robotic welders have a perfect tilt-angle with optimal welding speeds, creating precise welds that are repeatable. This allows the work they do to be extremely precise and high in quality, leading to fewer rejected parts.
Less Material Usage & Costs – Robots are programmed to use the precise amount of material needed for a given job. Over time, this creates less waste and easier clean-up. They also use fewer consumables like gas, base metal, electricity, flux, and more.
Improved Safety – Since weld cells naturally present safety hazards such as sparking, flashing, create fumes, and heat, the use of a robotic welder takes operators away from these associated risks. This also helps to reduce any potential injuries or lost time accidents related to the welding of smaller parts.
Programming – The addition of robot welders requires the addition of trained programming personnel, allowing employees opportunities for personal growth and development. We have actually hired more employees with the acquisition of our robotic welder!
Examples Of Harmony’s Robotic Welder Efficiency
Our Robotic Welder Specialists, Engineers, and Production Team have been busy creating jigs and programming our robotic welder for a variety of jobs.
Some examples of these include baler pivot shafts, platen guides, clean out rods, and compactor guide islands. With each part, the robot is able to turn out consistently high quality parts in a fraction of the time it used to take.
This picture shows how our robotic welder was able to produce eighty of our C300 Stationary Compactor guide islands in only 3 ½ hours!
Our dedicated crew will continue to add jigs for these types of parts in the coming months to make our robotic welder even more efficient!
Contact Us To Learn More Today!
Interested in learning more about our automated manufacturing processes or any of our over 40 models of recycling balers, trash compactors, or full product destruction machines? We would love to hear from you! Give us a call at (507) 886-6666 or fill out this simple form to contact us today!